ГОСТ Р 59248–2020 Угли бурые каменные. Методы отбора и подготовки проб
Чем больше проба по массе, тем выше точность и меньше влияние человеческого фактора.
ГОСТ Р 59248–2020
НАЦИОНАЛЬНЫЙ СТАНДАРТ РОССИЙСКОЙ ФЕДЕРАЦИИ
УГЛИ БУРЫЕ, КАМЕННЫЕ, АНТРАЦИТ, ГОРЮЧИЕ СЛАНЦЫ И УГОЛЬНЫЕ БРИКЕТЫ
Методы отбора и подготовки проб для лабораторных испытаний
Brown coals, hard coals, anthracite, combustible shales and coal briquettes. Methods of sampling and preparation of samples for laboratory tests
ОКС 75.160.10
Дата введения 2021-04-01
Предисловие
1 РАЗРАБОТАН Федеральным государственным автономным образовательным учреждением высшего образования “Национальный исследовательский технологический университет “МИСиС” (НИТУ “МИСиС”)
2 ВНЕСЕН Техническим комитетом по стандартизации ТК 179 “Топливо твердое минеральное”
3 УТВЕРЖДЕН И ВВЕДЕН В ДЕЙСТВИЕ
4 ВВЕДЕН ВПЕРВЫЕ
Правила применения настоящего стандарта установлены в “. Информация об изменениях к настоящему стандарту публикуется в ежегодном (по состоянию на 1 января текущего года) информационном указателе “Национальные стандарты”, а официальный текст изменений и поправок — в ежемесячном информационном указателе “Национальные стандарты”. В случае пересмотра (замены) или отмены настоящего стандарта соответствующее уведомление будет опубликовано в ближайшем выпуске ежемесячного информационного указателя “Национальные стандарты”. Соответствующая информация, уведомление и тексты размещаются также в информационной системе общего пользования — на официальном сайте Федерального агентства по техническому регулированию и метрологии в сети Интернет (www.gost.ru)
1 Область применения
Настоящий стандарт распространяется на угли (бурые, каменные и антрацит), горючие сланцы и угольные брикеты (далее — топливо) с крупностью кусков до 300 мм (для горючих сланцев в особых случаях — до 400 мм) и устанавливает методы отбора проб из потока, железнодорожных вагонов, судов, других транспортных средств, складов, а также методы подготовки проб для лабораторных физических испытаний и химического анализа.
2 Нормативные ссылки
В настоящем стандарте использованы нормативные ссылки на следующие стандарты:
Топливо твердое. Ситовый метод определения гранулометрического состава
Сетки с квадратными ячейками из стальной рифленой проволоки. Технические условия
Сетки проволочные тканые с квадратными ячейками. Технические условия
Угли. Термины и определения
Уголь. Обогащение. Термины и определения
Топливо твердое. Методы определения погрешности отбора и подготовки проб
Угли бурые, каменные и антрацит. Номенклатура показателей качества
Угли и продукты их переработки. Отбор проб со склада
Уголь каменный и кокс. Механический отбор проб. Часть 7. Методы определения прецизионности отбора, подготовки и испытания проб
Уголь каменный и кокс. Механический отбор проб. Часть 8. Методы определения систематической погрешности
(ИСО 3310–1‑90) Сита лабораторные из металлической проволочной сетки. Технические условия
Топливо твердое минеральное. Определение общей влаги
Весы неавтоматического действия. Часть 1. Метрологические и технические требования. Испытания
Уголь каменный и кокс. Ручной отбор проб
Примечание — При пользовании настоящим стандартом целесообразно проверить действие ссылочных стандартов в информационной системе общего пользования — на официальном сайте Федерального агентства по техническому регулированию и метрологии в сети Интернет или по ежегодному информационному указателю “Национальные стандарты”, который опубликован по состоянию на 1 января текущего года, и по выпускам ежемесячного информационного указателя “Национальные стандарты” за текущий год. Если заменен ссылочный стандарт, на который дана недатированная ссылка, то рекомендуется использовать действующую версию этого стандарта с учетом всех внесенных в данную версию изменений. Если заменен ссылочный стандарт, на который дана датированная ссылка, то рекомендуется использовать версию этого стандарта с указанным выше годом утверждения (принятия). Если после утверждения настоящего стандарта в ссылочный стандарт, на который дана датированная ссылка, внесено изменение, затрагивающее положение, на которое дана ссылка, то это положение рекомендуется применять без учета данного изменения. Если ссылочный стандарт отменен без замены, то положение, в котором дана ссылка на него, рекомендуется применять в части, не затрагивающей эту ссылку.
3 Термины и определения
В настоящем стандарте применены термины по , и , а также следующий термин с соответствующим определением:
3.1 базовая погрешность опробования: Норматив контроля, числовое значение которого является критерием для признания конкретного показателя качества соответствующим или несоответствующим установленным требованиям с учетом отбора, подготовки и анализа проб.
4 Общие положения
4.1 Отбор объединенных проб проводят от каждой партии топлива. При регулярных поставках допускается по согласованию сторон периодическое опробование партий топлива в соответствии с приложением А.
4.2 Отбор проб проводят:
- из потока топлива в местах его перепада или с поверхности транспортирующего устройства;
- от неподвижного слоя топлива, погруженного в транспортные средства;
- от топлива со склада.
4.3 Базовые погрешности опробования (отбора, подготовки и анализа проб) углей и брикетов определяют по величине зольности на сухое топливо, массовой доли общей влаги на рабочее состояние топлива или низшей теплоты сгорания на рабочее состояние топлива (а для сланцев — только низшей теплоты сгорания на рабочее состояние топлива) при доверительной вероятности Р=0,95 в соответствии с таблицей 1.
Базовые погрешности, приведенные в таблице 1, применяют для всех видов опробования по настоящему стандарту.
Таблица 1 — Базовые погрешности опробования
Наименование показателя | Значение | Базовая погрешность опробования ![]() ![]() ![]() |
Зольность ![]() ![]() массовая доля общей влаги на |
До 20% | ±10% отн. |
рабочее состояние топлива![]() ![]() |
Более 20% | ±2% абс. |
Низшая теплота сгорания на рабочее состояние топлива![]() ![]() |
До 12,56 МДж/кг
(до 3000 ккал/кг) |
±0,63 МДж/кг
(±150 ккал/кг) |
Более 12,56 МДж/кг
(более 3000 ккал/кг) |
±0,84 МДж/кг
(±200 ккал/кг) |
4.4 Отбор проб следует проводить ручным или механизированным способом с применением пробоотборников, соответствующих требованиям настоящего стандарта.
Точечные пробы, отбираемые в объединенную пробу, должны быть равномерно распределены по всему объему партии топлива.
4.5 Количество точечных проб n, отбираемых в объединенную пробу от партии каменных углей и антрацитов массой до 1000 т или от партии бурых углей, горючих сланцев и брикетов массой до 2500 т для определения зольности, массовой доли общей влаги и низшей теплоты сгорания с погрешностью, не превышающей величин, указанных в таблице 1, приведено в таблице 2.
Таблица 2 — Количество точечных проб, отбираемых в объединенную пробу
Вид топлива | Количество точечных проб, не менее |
Угли обогащенные (рассортированные и не рассортированные), брикеты | 16 |
Угли рядовые и горючие сланцы | 32 |
Примечания
1 Для товарных классов угля, полученных рассортировкой рядового угля, а также для углей после породовыборки количество точечных проб определяют так же, как и для рядового угля. Для промежуточных продуктов обогащения количество точечных проб определяют так же, как и для обогащенного угля.
2 От партии топлива массой до 500 т в объединенную пробу отбирают 16 точечных проб независимо от вида топлива.
3 От партии топлива, состоящего из одного железнодорожного вагона, в объединенную пробу отбирают 8 точечных проб независимо от вида топлива.
4 Проверку погрешности опробования и необходимого количества точечных проб проводят по .
При отборе объединенных проб от партий более 1000 т для каменных углей и антрацитов и более 2500 т для бурых углей, горючих сланцев и брикетов количество точечных проб
(1)
где M — масса опробуемой партии топлива, т;
C — 1000 т — для каменных углей и антрацитов или 2500 т — для бурых углей, горючих сланцев и брикетов.
Результат расчета округляют до ближайшего большего целого числа.
По согласованию между поставщиком и потребителем допускается проводить отбор проб с погрешностью опробования, которая больше или меньше указанной в таблице 1. В этом случае количество точечных проб
(2)
(3)
где
Результат расчета округляют до ближайшего большего целого числа.
4.6 Минимальную массу точечных проб m, кг, отбираемых в объединенную пробу, вычисляют по формуле
m=0,06D,
(4)
где D — максимальный размер кусков, мм.
За максимальный размер кусков рядового топлива условно принимают размер ячейки сита, на котором при просеивании по надрешетный продукт составляет не более 5%.
За максимальный размер кусков топлива, полученного путем рассортировки по классам крупности, принимают верхний предел крупности этого класса.
Масса точечных проб брикетов должна быть не менее 3 кг.
4.7 Если масса точечной пробы в четыре и более раз превышает минимально необходимую (например, при отборе проб из потоков большой мощности по всему сечению, при отборе проб из вагонов или других транспортных средств грейферными установками), допускается сокращение массы первоначально отобранных точечных проб без предварительного дробления до значений, указанных в 4.6.
5 Оборудование для отбора и подготовки проб
5.1 Оборудование для отбора проб
5.1.1 Механические пробоотборники для отбора проб в местах перепада потока, непосредственно с транспортерных лент, от топлива, погруженного в железнодорожные вагоны и другие транспортные средства.
5.1.2 Приспособления для отбора проб вручную.
5.2 Требования к оборудованию для отбора проб
5.2.1 Ширина раскрытия отбирающего устройства пробоотборника должна превышать размер максимальных кусков опробуемого топлива не менее чем в 2,5 раза при отборе проб на перепадах потока, не менее чем в 2 раза при отборе проб с конвейерных лент и не менее чем в 1,5 раза при отборе проб из транспортных средств.
Во всех случаях ширина раскрытия должна быть не менее 50 мм.
5.2.2 Вместимость ковшовых отбирающих устройств должна быть такой, чтобы при отборе точечных проб исключить их переполнение.
5.2.3 Отбирающее устройство должно полностью освобождаться от материала пробы после окончания отбора.
5.2.4 Отбирающие устройства для отбора проб из потока должны за одно или несколько пересечений отбирать точечные пробы по всему поперечному сечению.
5.2.5 Буровой пробоотборник для отбора проб из погруженного в транспортные средства топлива должен отбирать точечные пробы на глубину не менее 3/4 высоты погруженного топлива, а грейферный — не менее 0,4 м от поверхности погруженного топлива.
Контрольные испытания всех пробоотборников проводят в соответствии с , и .
При внедрении новых типов пробоотборников, а также введении впервые в эксплуатацию или выходе из ремонта традиционно используемых на предприятии пробоотборников, их испытывают с целью определения представительности отбираемых ими проб.
5.2.6 Приспособления для отбора проб вручную рекомендуется применять с учетом типов оборудования, приведенных в пунктах 6.1 и 6.2 .
5.3 Оборудование для обработки проб
5.3.1 Машины для обработки объединенных проб, обеспечивающие приготовление не менее двух лабораторных проб.
5.3.2 Машины для обработки объединенных проб, обеспечивающие одновременное приготовление одной лабораторной и не менее двух аналитических проб.
5.3.3 Машины для обработки лабораторных проб, обеспечивающие приготовление не менее двух аналитических проб.
5.3.4 Дробилки для дробления объединенных проб.
5.3.5 Мельницы для измельчения лабораторных проб.
5.3.6 Делители и сократители для сокращения первоначальной массы проб и деления сокращенной части пробы на требуемое количество экземпляров.
5.3.7 Механические устройства и набор сит для рассева проб по .
5.3.8 Противни различных размеров из коррозионно-стойкого и теплостойкого материала для подсушивания, сокращения и деления проб.
5.3.9 Шкафы сушильные с регулируемой принудительной или естественной вентиляцией и с терморегулятором, обеспечивающие устойчивую температуру нагрева в интервалах 35°С‑55°С и 105°С‑135°С.
5.3.10 Весы по .
5.3.11 Лабораторные сита из сеток с размерами ячеек 0,2 и 1 мм по или . Сита из сеток с размерами ячеек 1,6; 3; 10; 13; 20 и 25 мм по .
5.4 Требования к оборудованию для обработки проб
5.4.1 Дробилки и мельницы должны обеспечивать заданную крупность дробления и измельчения.
5.4.2 Сократители должны сокращать массу пробы в заданном соотношении, не нарушая ее представительности.
5.4.3 Механические делители (сократители) должны обеспечивать равномерное перемешивание пробы и деление на требуемое количество экземпляров. При этом масса отдельных экземпляров разделенной пробы не должна отличаться от среднего значения более чем на ±10%, а разница в зольности и массовой доле влаги не должна превышать пределов воспроизводимости, предусмотренных стандартами на соответствующие методы испытаний.
Допускается перемешивание, сокращение и деление пробы вручную на требуемое количество экземпляров без нарушения ее представительности и с соблюдением условия расхождения между массами и результатами анализов дубликатов проб. При ручном перемешивании, сокращении и делении пробы рекомендуется использовать оборудование и основные принадлежности по пункту 8.3.5 .
5.4.4 Контрольные испытания машин для подготовки проб, дробилок и мельниц следует проводить не реже одного раза в месяц путем рассева измельченного ими топлива. При установленном верхнем пределе крупности измельченного материала, равном 1 мм и более, остаток на сите с квадратными отверстиями размером, равным установленному пределу крупности, не должен превышать 3% массы, взятой для рассева.
При установленном верхнем пределе крупности измельченного материала, равном 0,2 мм, остаток на сите с квадратными отверстиями (0,2х0,2) мм по не должен превышать 1% массы, взятой для рассева.
6 Отбор проб
6.1 Отбор проб из потока
6.1.1 Из потока пробы отбирают при погрузке или разгрузке вагонов, судов, автомашин и других транспортных средств, а также при транспортировании топлива конвейерами непосредственно потребителям.
6.1.2 Отбор проб из потока проводят механизированным способом с применением имеющихся в наличии пробоотборников и приспособлений, отвечающих требованиям 5.2.
6.1.3 Точечные пробы отбирают через равные интервалы времени.
Интервал времени t, мин, через который следует отбирать точечные пробы, вычисляют по формуле
(5)
где M — масса опробуемой партии топлива, т;
Q — производительность (мощность) опробуемого потока, т/ч;
n — количество точечных проб, которое необходимо отобрать в объединенную пробу.
6.1.4 При отборе проб из потока мощностью более 600 т/ч допускается деление его на части, при этом отбор точечных проб проводят поочередно из каждой части потока через постоянные интервалы времени. Общее число точечных проб, отобранных от всех частей потока, должно соответствовать требованиям 4.5.
6.1.5 При отборе проб с поверхности движущегося конвейера точечные пробы необходимо отбирать по всему сечению потока перпендикулярно или под углом к его оси так, чтобы отбирающее приспособление не создавало подпора движущемуся топливу.
6.1.6 Отбор проб топлива, транспортируемого ковшовым конвейером (элеватором), проводят из потока после выгрузки ковшей согласно 6.1.3 или отдельными ковшами. При этом топливо в одном ковше считается точечной пробой. Если масса точечной пробы больше минимальной, установленной в 4.6, допускается ее сокращение.
6.2 Отбор проб с поверхности остановленного ленточного конвейера
Отбор проб с поверхности остановленного ленточного конвейера проводят, главным образом, для проверки всех способов отбора проб. Точечные пробы отбирают с помощью приспособления (рамы), погружаемого в массу топлива до транспортирующей поверхности, перпендикулярно к направлению движения потока. В точечную пробу включают все топливо, попавшее внутрь приспособления, и отдельные крупные куски, попавшие под правую сторону приспособления (по направлению движения потока). Рама должна представлять собой две параллельные, вертикально расположенные стенки, отстоящие одна от другой на расстояние не менее двух размеров максимального куска и жестко соединенные между собой. Раму следует устанавливать в строго определенном месте конвейера, максимально удаленном от мест перепадов. Рекомендуется использовать конструкции рамы в соответствии с пунктами 6.1 и 6.2 .
6.3 Отбор проб из железнодорожных вагонов, вагонеток, автомашин
6.3.1 От топлива, погруженного в железнодорожные вагоны, вагонетки, автомашины, пробы отбирают в тех случаях, когда невозможно осуществить отбор проб из потока.
6.3.2 Отбор точечных проб проводят в определенных точках, равномерно распределенных по поверхности топлива в вагоне, вагонетке, автомашине. Отбор точечных проб вручную проводят со дна лунок, выкопанных на глубину не менее 0,4 м от поверхности погруженного топлива, а для брикетов — не менее 0,2 м.
При крупности топлива не более 25 мм отбор точечных проб допускается проводить зондированием в соответствии с указаниями .
Топливо берут без выбора, включая в точечную пробу уголь, сростки, породу. Расположение мест отбора точечных проб из вагона должно соответствовать схеме, приведенной на рисунке 1, из автомашин и вагонеток — схеме на рисунке 2.
Расчет количества точечных проб от партий топлива, представленных транспортными единицами различной грузоподъемности, приведен в приложении Б.
Примечания
1 При отборе проб вручную от топлива крупностью до 100 мм точечные пробы отбирают в один прием, а от топлива крупностью более 100 мм допускается проводить набор точечных проб в 2–3 приема, обеспечивая при этом требуемую массу точечной пробы.
2 При отборе проб из единичных вагонов точечные пробы отбирают по схеме, изображенной на рисунке 1, в шахматном порядке.
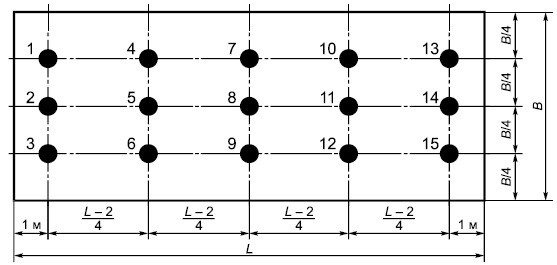
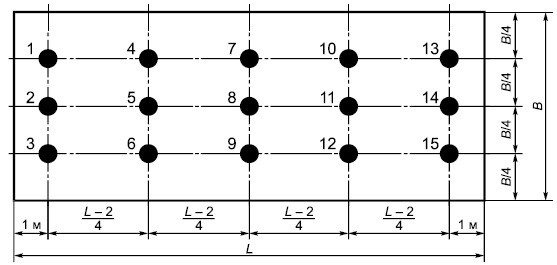
Рисунок 1 — Схема отбора точечных проб из единичных вагонов
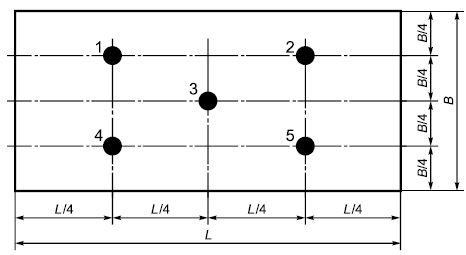
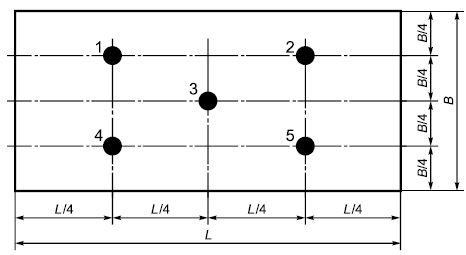
Рисунок 2 — Схема отбора точечных проб из автомашин и вагонеток
6.3.3 Для отбора проб из железнодорожных вагонов, автомашин и автоприцепов допускается применять промышленные грейферные установки, при этом ширина раскрытия челюстей грейферов должна быть не менее половины ширины вагона, а ширина челюстей — не менее чем в 2,5 раза больше размера максимальных кусков опробуемого топлива.
При отборе проб грейферными установками каждая точечная проба представляет собой один грейферный захват. При этом необходимо соблюдать указанную ниже последовательность в выполнении отдельных операций:
- расположение точек в вагоне намечают в соответствии со схемой, изображенной на рисунке 3а, а в автомашине и автоприцепе — в соответствии со схемой, изображенной на рисунке 3б;
- отбор точечных проб в каждой точке проводят погружением грейфера в топливо не менее чем на 0,4 м при полном раскрытии его челюстей;
- отобранную грейфером точечную пробу разгружают в накопительную емкость, из которой она равномерным потоком поступает на механический пробоотборник;
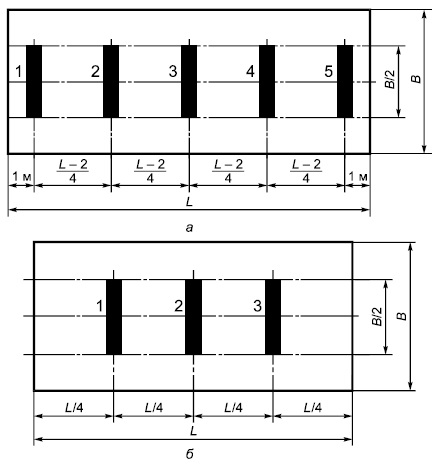
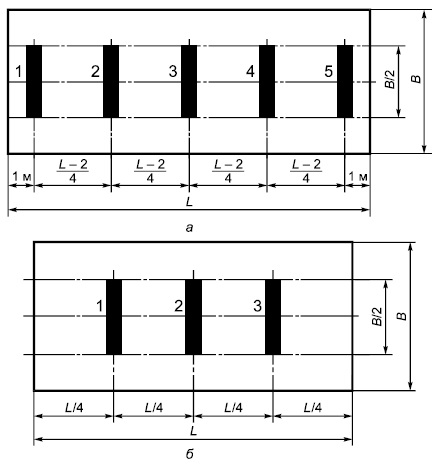
а — схема расположения точек в вагоне; б — схема расположения точек в автомашине и автоприцепе
Рисунок 3 — Схема расположения точек при отборе проб грейфером
- от каждой точечной пробы топлива, отобранной грейфером, с помощью механического пробоотборника необходимо отобрать не менее трех точечных проб. Масса точечных проб, отбираемых механическим пробоотборником, должна соответствовать требованиям 4.6.
6.3.4 При использовании буровых пробоотборников схема расположения точек должна соответствовать рисункам 1 и 2.
6.4 Отбор проб из судов и барж
6.4.1 Отбор проб из судов и барж проводят с помощью грейферных установок только в тех случаях, когда невозможно применить отбор проб из потока или из вагонов и вагонеток.
Количество точечных проб, отбираемых в объединенную пробу, должно соответствовать количеству, указанному в 4.5.
Периодичность отбора точечных проб
(6)
где M - масса опробуемого топлива, т;
q — грузоподъемность грейфера, т;
Пример
В судно должно быть погружено 4000 т необогащенного каменного угля. Загрузку судна проводят грейфером грузоподъемностью 5 т.
Согласно 4.5 и таблице 2 количество точечных проб в объединенной пробе должно быть не менее
Периодичность отбора точечных проб
В объединенную пробу следует брать топливо из каждого двенадцатого грейфера.
6.4.2 При транспортировании судном топлива одного типа (марки) или класса крупности от всего загруженного топлива отбирают одну объединенную пробу. Количество точечных проб, отбираемых от топлива, находящегося в каждом трюме, должно быть пропорционально количеству топлива, погруженного в соответствующий трюм.
При транспортировании судном топлива различных типов (марок) или классов крупности топливо, находящееся в каждом трюме, считают отдельной партией, от которой отбирают объединенную пробу.
6.4.3 Отбор проб непосредственно из барж допускается только в тех случаях, когда нет возможности провести отбор проб из потока или с помощью грейфера.
Места отбора точечных проб равномерно распределяют по всей площади баржи, как это изображено на рисунке 4. Если высота слоя топлива, погруженного в трюм, менее 4 м, то все точечные пробы отбирают из верхнего слоя.
Если высота слоя топлива, погруженного в трюм, более 4 м, то точечные пробы отбирают послойно в два приема: нечетные точечные пробы отбирают после снятия верхнего слоя, а четные точечные пробы отбирают примерно с половины глубины погруженного топлива.
6.4.4 При отборе проб из судов и барж с помощью грейфера глубина погружения челюстей грейфера в топливо должна быть не менее 0,4 м. Каждый грейфер, топливо в котором предназначено в пробу, разгружают в накопительную емкость, из которой топливо равномерным потоком подается на механический пробоотборник. Количество отбираемых пробоотборником точечных проб должно соответствовать требованиям, установленным в 4.5, а их масса должна быть не менее массы, установленной в 4.6.
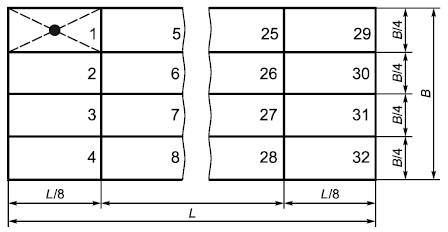
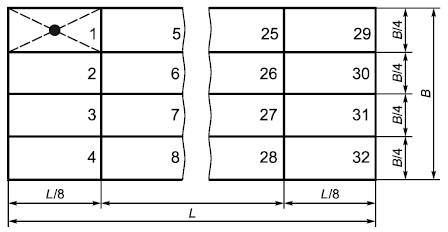
Рисунок 4 — Схема отбора проб из барж
6.4.5 При невозможности выполнения требований отбора точечных проб с применением грейферной установки, указанных в 6.3.3 и 6.4.4, необходимо каждый грейфер, из которого топливо предназначено в пробу, разгрузить на специальную предварительно зачищенную площадку. От выгруженного топлива вручную отбирают пять точечных проб в соответствии с 6.3.2 по схеме, изображенной на рисунке 5.
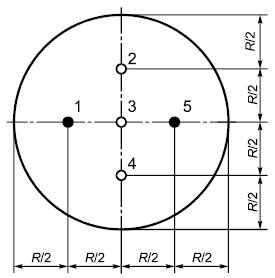
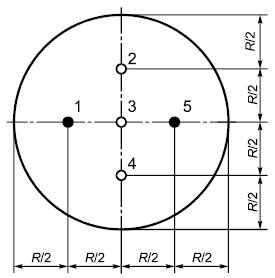
Рисунок 5 — Схема отбора проб вручную из точечной пробы, выгруженной грейфером на площадку
6.5 Отбор проб со склада
Отбор проб со склада проводят по .
7 Обработка проб и подготовка их для проведения испытаний
7.1 Общие положения
Обработка проб включает в себя последовательные операции дробления, сокращения, измельчения и деления пробы с целью доведения ее до состояния, пригодного для выполнения соответствующего испытания. Перед каждой операцией сокращения (деления) следует проводить тщательное перемешивание пробы.
Операции обработки проб проводят механизированным способом с применением машин и механизмов, соответствующих требованиям 5.4. Допускается обработку и сокращение проб проводить вручную с учетом рекомендаций .
При обработке проб брикетов для общего анализа используют остатки проб брикетов после их испытания на механическую прочность и те брикеты из объединенной пробы, которые не подвергались испытанию. Для определения общей влаги остатки проб брикетов после их испытания на механическую прочность использовать не допускается.
7.2 Обработка объединенных проб
Объединенные пробы обрабатывают по мере отбора отдельных точечных проб или после окончания отбора всех точечных проб, составляющих объединенную пробу. При этом следует предпринимать меры, предотвращающие потери материала пробы и изменение ее свойств.
В тех случаях, когда объединенную пробу составляют после дробления и сокращения точечных проб, масса сокращенных точечных проб должна быть пропорциональна их первоначальной массе, но не менее указанной в 4.6.
7.3 Приготовление лабораторных проб
7.3.1 Приготовление лабораторных проб в одну стадию
Объединенную пробу, полученную по 7.2, измельчают до крупности от 0 до 3 мм или от 0 до 10 (13) мм. С помощью сократителя или вручную методом выборки выделяют необходимое количество лабораторных проб, масса каждой из которых должна быть не менее массы, указанной в 7.3.4.
7.3.2 Приготовление лабораторных проб в две стадии
Если оборудование не позволяет провести обработку объединенной пробы, полученной по 7.2, в одну стадию, обработку проводят в две стадии.
При обработке объединенных проб в две стадии сначала пробы дробят до крупности не более 20 (25) или 10 (13) мм и сокращают в соответствии с 7.3.4.
Далее пробы дробят до необходимой крупности для получения лабораторных проб аналогично 7.3.1.
7.3.3 Обработка проб топлива с высокой влажностью
Для топлива с такой влажностью, при которой дробление объединенной пробы механическим способом затруднено или вообще невозможно, объединенную пробу подсушивают на воздухе или в сушильном шкафу (5.3.9) до состояния, позволяющего проводить ее дальнейшую обработку (в одну или две стадии), либо минимально дробят крупные куски до крупности, позволяющей сократить пробу в соответствии с 7.4.3 или (приложение А). Температуру сушки пробы следует выбирать с учетом требований 7.4.2.
При подсушивании всей объединенной пробы (или ее сокращенной части) фиксируют потерю влаги до достижения воздушно-сухого состояния топлива и используют это значение для расчета внешней влаги по .
7.3.4 Сокращение объединенной пробы после дробления
Сокращение объединенной пробы, полученной по 7.3.1, 7.3.2 или 7.3.3 после дробления, проводят с использованием делителей (сократителей) до минимальных масс, указанных в таблице 3.
Таблица 3 — Минимальные массы сокращенных проб после дробления объединенной пробы
Максимальный размер кусков в дробленой пробе, мм | Минимальная масса пробы после сокращения, кг | |
Угли обогащенные (рассортированные и не рассортированные), брикеты | Рядовой уголь и горючие сланцы | |
20 (25)![]() ![]() ![]() ![]() ![]() |
5 | 30 |
10 (13)![]() ![]() ![]() ![]() ![]() |
1,5 | 10 |
3 (5)![]() ![]() ![]() ![]() ![]() |
0,65 | 2 |
1,6 | 0,2 | 1 |
1,0 | 0,15 | 0,6 |
![]() ![]() ![]() ![]() ![]() |
Чем больше проба по массе, тем выше точность и меньше влияние человеческого фактора.
Для товарных классов угля, полученных рассортировкой рядового угля, а также для углей после породовыборки минимальные массы сокращенных проб определяют как для рядового угля. Для промежуточных продуктов обогащения минимальные массы сокращенных проб определяют как для обогащенного угля.
При сокращении пробы вручную или ковшовым сократителем в сокращенную часть необходимо отбирать не менее 50 точечных проб массой не менее 0,10 кг каждая для крупности 0–20 (25) мм, не менее 0,03 кг — для крупности 0–10 (13) мм и не менее 0,01 кг — для крупности 0–3 (5) мм.
Для других значений крупности, не предусмотренных таблицей 3, минимальную массу сокращенной пробы у, кг, вычисляют следующим образом:
- для обогащенных углей (рассортированных и не рассортированных), промежуточных продуктов обогащения и брикетов — по формуле
(7)
- для рядовых углей, горючих сланцев, товарных классов угля, полученных рассортировкой рядового угля, а также углей после породовыборки — по формуле
(8)
где x — максимальный размер кусков после дробления, мм.
7.3.5 Для определения показателей качества, установленных в , лабораторную пробу измельчают до крупности, регламентируемой в стандартах на соответствующие методы испытаний. При необходимости детальной характеристики углей с учетом специальных требований в зависимости от направлений использования, по согласованию с потребителем определяют дополнительные показатели (не указанные в ), при этом лабораторную пробу измельчают до крупности, указанной в соответствующем документе на метод испытания.
При приготовлении проб для испытаний после измельчения до требуемой крупности пробу просеивают через сито (см. 5.3.11) с соответствующим размером ячеек; весь надрешетный продукт подвергают дополнительному измельчению до прохождения через то же сито и добавляют к подрешетному продукту.
7.4 Приготовление аналитических проб для лабораторных испытаний
7.4.1 Сокращенную лабораторную пробу, полученную по 7.3, делят на требуемое количество экземпляров лабораторной пробы.
Сокращение и деление лабораторной пробы на требуемое количество экземпляров допускается проводить одновременно. Масса каждого экземпляра лабораторной пробы определенной крупности для различных испытаний должна быть не менее указанной в 7.3.4.
Для определения показателей качества может быть использован любой экземпляр лабораторной пробы.
Если обработку лабораторных проб до аналитических проводят на предприятии, где осуществляется отбор проб, в лабораторию направляют лабораторную пробу в герметичной таре для определения массовой доли влаги и аналитическую пробу в герметичной таре для проведения общего анализа.
Если обработку лабораторной пробы до аналитической проводят в лаборатории, то для определения массовой доли влаги и общего анализа в лабораторию направляют только один экземпляр лабораторной пробы в герметичной таре. Общая масса такой лабораторной пробы должна быть не менее указанной в таблице 3 и обеспечивать проведение необходимых испытаний.
Если состояние упаковки не соответствует требованиям раздела 8, пробу бракуют и ставят в известность лицо, ответственное за доставку проб.
7.4.2 Если в одном экземпляре лабораторной пробы необходимо определить массовую долю общей влаги и другие показатели качества, то сначала из лабораторной пробы отбирают навески для определения массовой доли общей влаги. Каждую навеску набирают из различных мест, равномерно распределенных по всему объему пробы.
Пробу с влажностью, препятствующей разделению частиц, после отбора навесок для определения общей влаги высыпают на противень (см. 5.3.8) такого размера, чтобы толщина слоя составляла не более 10 мм. Пробу сушат на воздухе или в сушильном шкафу (см. 5.3.9) до видимого отделения частиц топлива друг от друга. При подсушивании в сушильном шкафу противень устанавливают в предварительно нагретый сушильный шкаф и выдерживают при температуре от 30°С до 55°С (медленная подсушка). Допускается ускоренная подсушка при температуре от 105°С до 135°С, если предварительно установлено, что она не оказывает влияние на определяемые показатели качества углей.
7.4.3 Подсушенную и охлажденную на воздухе лабораторную пробу измельчают в соответствующих машинах для получения из нее аналитической пробы.
Рекомендуется для приготовления аналитической пробы использовать лабораторную пробу с размером частиц менее 3 мм.
При приготовлении аналитическую пробу измельчают до полного ее прохождения через сито с размером ячеек 0,2 мм (см. 5.3.11), повторно измельчая остаток на сите и добавляя его в пробу.
7.4.4 Полученную по 7.4.3 аналитическую пробу перемешивают и делителем сокращают до массы не менее 0,085 кг.
При отсутствии делителя допускается сокращать аналитическую пробу вручную с помощью крестовины, делительной решетки или путем набора точечных проб из различных мест, равномерно расположенных по всему объему пробы.
7.5 Помещения для обработки проб должны быть хорошо освещены, защищены от сквозняков, попадания прямых солнечных лучей, излучающих тепло поверхностей, а также должны быть оборудованы приточно-вытяжной вентиляцией и обособлены от других производственных помещений.
8 Упаковка и маркировка проб
8.1 Для транспортировки лабораторные и аналитические пробы помещают в тару, отвечающую следующим требованиям:
- тара должна быть прочной, чтобы обеспечить сохранность проб при хранении и транспортировке;
- тара должна быть изготовлена из материалов, исключающих взаимодействие с пробой (в том числе коррозионно-стойких);
- тара должна быть герметично закрытой особенно тщательно, если проба предназначается для определения содержания влаги;
- объем тары должен соответствовать массе пробы, т.е. тара должна быть заполнена не более чем на 3/4 объема, чтобы иметь возможность тщательно перемешать пробу;
- не допускается хранить один экземпляр пробы в нескольких емкостях.
Взвешивают пустую тару с крышкой и помещают в нее пробу. Один экземпляр этикетки, защищенный водонепроницаемой пленкой, помещают в тару вместе с пробой и герметично закрывают тару. Второй экземпляр этикетки надежно прикрепляют снаружи. Тару опечатывают (пломбируют) и снова взвешивают. Взвешивания проводят на весах по ГОСТ 53228* с точностью до 1 г.
8.2 Этикетки должны содержать следующую информацию:
- номер пробы;
- дату и смену (время) отбора и обработки пробы;
- наименование пробы (товарная, контрольная, исследовательская и т.д.);
- массу тары и массу брутто лабораторной или аналитической пробы;
- наименование предприятия;
- вид продукции;
- марку и сорт топлива;
- массу партии топлива, от которой отобрана проба;
- подпись лица, ответственного за отбор и обработку пробы.
Приложение А
(рекомендуемое)
Определение периодичности опробования товарного топлива
А.1 При периодическом опробовании отбор проб проводят не от всего количества топлива, отправляемого потребителю, а от части партии вагонов, входящих в поставку за определенный период времени (декаду, месяц, квартал, год) или в соответствии с графиком контроля на предприятии.
А.2 Периодическое опробование проводится предприятием-грузоотправителем или на пунктах контроля качества только при регулярных поставках топлива одному и тому же потребителю при согласии заинтересованных сторон.
А.3 Периодическое опробование устанавливают отдельно для каждого вида продукции, отгружаемого предприятием.
А.4 Исходными данными для расчета доли продукции, подлежащей опробованию, являются:
- данные о массе и зольности топлива каждой отгруженной партии не менее чем за два предшествующих месяца;
- количество единиц продукции (партий, вагонов и т.д.) за месяц согласно плану поставки;
- допустимая погрешность опробования за период поставки.
А.5 Данные об отгруженной продукции за предшествующий период представляют по следующей форме (заполнена для примера).
Шахта (ОФ)________________________ производственное объединение_____________________
месяц____________________________ год_______________
Порядковые номера партий топлива | Масса партий, т | Зольность, % |
1 | 620 | 24,1 |
2 | 732 | 25,2 |
3 | 867 | 23,8 |
… | … | … |
74 | 1022 | 23,1 |
Всего | 59370 | 24,1 |
По представленным данным проводят расчет средневзвешенной зольности всех отгруженных партий и размаха колебаний зольности.
Размах колебаний зольности R определяют как разность между средним из трех наибольших и средним из трех наименьших значений зольности отдельных партий продукции.
Например, если наибольшие зольности партий за рассматриваемый период составили 29,8%; 26,3% и 26,0% (средняя наибольшая 27,4%), а наименьшие — 16,9%; 16,7% и 15,9% (средняя наименьшая 16,5%), то размах колебаний зольности R=27,4–16,5=10,9%.
А.6 Общее количество поставляемых за определенный период единиц продукции принимают равным числу вагонов, соответствующих плановой поставке, если периодическое опробование осуществляется по отдельным вагонам, числу партий, если периодическое опробование осуществляется по отдельным партиям, или числу смен, если периодическое опробование осуществляется по отдельным сменам. Периодическое опробование отдельных партий и смен проводят только из потока.
А.7 Допустимую погрешность за период поставки
А.8 Расчет доли опробуемой продукции проводят в следующем порядке.
А.8.1 Вычисляют неоднородность или среднее квадратическое отклонение зольности партий угля
(А.1)
где
А.8.2 Вычисляют погрешность оценки средней зольности за период поставки
(А.2)
где t — нормированное отклонение, равное 2, что соответствует доверительной вероятности 95,0%;
N — общее число отгружаемых данному потребителю единиц продукции (вагонов, партий, смен);
n — число точечных проб, отбираемых от каждой единицы продукции.
Если
А.8.3 Определяют по графику (см. рисунок А.1) погрешность периодического опробования
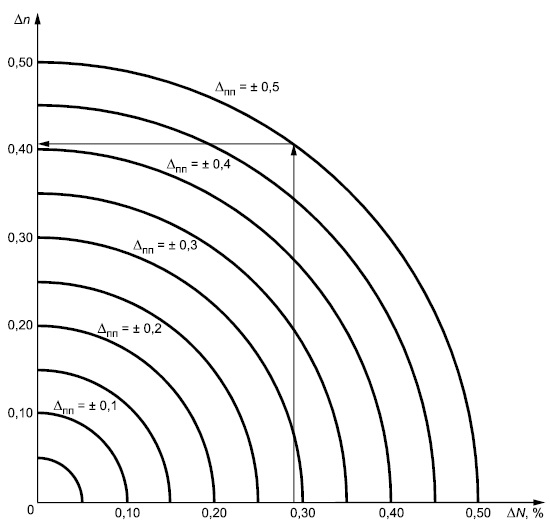
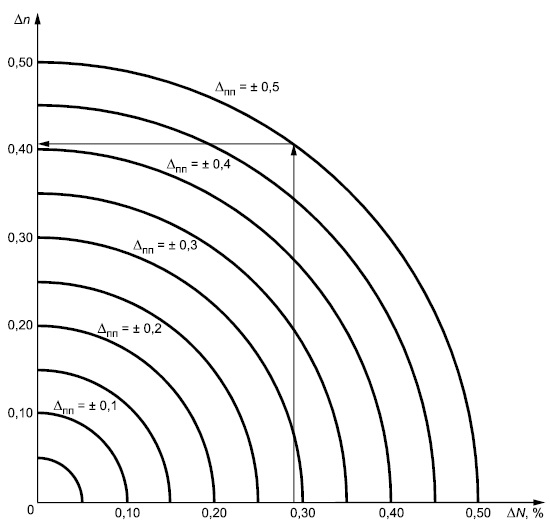
Рисунок А.1
А.8.4 Вычисляют нестабильность зольности угля
(А.3)
где R — размах колебаний зольности, %.
А.8.5 Рассчитывают параметр периодического опробования K по формуле
(А.4)
где B - коэффициент, определяемый по таблице А.1 в зависимости от нестабильности зольности
Таблица А.1 — Значения коэффициента В в зависимости от нестабильности зольности угля
![]() ![]() ![]() ![]() ![]() ![]() ![]() ![]() ![]() |
B | ![]() ![]() ![]() ![]() ![]() ![]() ![]() ![]() ![]() |
B |
0,3 | 1,300 | 2,7 | 0,129 |
0,4 | 0,970 | 2,8 | 0,124 |
0,5 | 0,780 | 2,9 | 0,119 |
0,6 | 0,642 | 3,0 | 0,116 |
0,7 | 0,550 | 3,1 | 0,110 |
0,8 | 0,478 | 3,2 | 0,107 |
0,9 | 0,423 | 3,3 | 0,104 |
1,0 | 0,379 | 3,4 | 0,099 |
1,1 | 0,376 | 3,5 | 0,095 |
1,2 | 0,313 | 3,6 | 0,094 |
1,3 | 0,287 | 3,7 | 0,090 |
1,4 | 0,267 | 3,8 | 0,087 |
1,5 | 0,246 | 3,9 | 0,085 |
1,6 | 0,231 | 4,0 | 0,082 |
1,7 | 0,216 | 4,1 | 0,080 |
1,8 | 0,202 | 4,2 | 0,076 |
1,9 | 0,192 | 4,3 | 0,075 |
2,0 | 0,182 | 4,4 | 0,073 |
2,1 | 0,172 | 4,5 | 0,071 |
2,2 | 0,163 | 4,6 | 0,070 |
2,3 | 0,155 | 4,7 | 0,068 |
2,4 | 0,148 | 4,8 | 0,066 |
2,5 | 0,141 | 4,9 | 0,065 |
2,6 | 0,136 | 5,0 | 0,063 |
А.8.6 Определяют по таблице А.2 долю единиц продукции d, подлежащей опробованию. Значение d принимают соответственно рассчитанному значению K или его ближайшему большему значению.
Таблица А.2 — Доля единиц продукции, подлежащей опробованию d, в зависимости от К
K | d | Примечание | |||
0,29 | 0,75 | Опробуют | 3/4 | единиц продукции | |
0,40 | 0,67 | Опробуют | 2/3 | единиц продукции | |
0,69 | 0,50 | Опробуют | половину | единиц продукции | |
1,10 | 0,33 | Опробуют | каждую | 3‑ю | единицу продукции |
1,39 | 0,25 | Опробуют | каждую | 4‑ю | единицу продукции |
1,61 | 0,20 | Опробуют | каждую | 5‑ю | единицу продукции |
1,79 | 0,167 | Опробуют | каждую | 6‑ю | единицу продукции |
1,95 | 0,143 | Опробуют | каждую | 7‑ю | единицу продукции |
2,08 | 0,125 | Опробуют | каждую | 8‑ю | единицу продукции |
2,20 | 0,111 | Опробуют | каждую | 9‑ю | единицу продукции |
2,30 | 0,100 | Опробуют | каждую | 10‑ю | единицу продукции |
А.8.7 Примеры расчета периодичности опробования товарного топлива
Пример
В течение предшествующих трех месяцев средняя зольность на сухое состояние угля шахты составила 18,2%, 18,6%, 17,2% (
Число точечных проб, отбираемых от каждой партии в соответствии с 4.5, равно 32.
Допустимая погрешность опробования за месяц
Расчет проводят в порядке, изложенном в А.8.
Определяют неоднородность угля по формуле (А.1)
Устанавливают погрешность определения зольности
Поскольку
По графику (рисунок А.1) для
Определяют нестабильность зольности
По таблице А.1 настоящего приложения определяют значение В=0,175 и рассчитывают параметр K по формуле (А.4)
По таблице А.2 находят d=0,5.
Таким образом, при заданных условиях можно опробовать не менее половины всех партий угля этой шахты.
Пример
Средняя зольность угля шахты составляет
Необходимо определить долю опробуемых вагонов при этих условиях.
Порядок расчета.
Определяют неоднородность угля
Определяют погрешность определения зольности за месяц
По графику (рисунок А.1) для
Определяют нестабильность зольности
По таблице А.1 определяют, что
По таблице А.2 находят d=0,33.
Таким образом, при заданных условиях может быть опробован каждый третий вагон.
А.9 Периодическое опробование может быть организовано с заданным циклом (например, при доле опробуемых партий d=0,33 опробуют каждую третью партию, начиная с первой, второй или третьей) или со случайным выбором номера партии, подлежащей контролю.
При опробовании с заданным циклом для того, чтобы периоды контроля совпадали с возможной периодичностью изменений качества, порядок контролируемых единиц продукции в период поставки может неоднократно нарушаться.
Например, при расчетной доле опробуемой продукции d=0,25 после опробования очередной, например 12‑й партии, контролируют не 16‑ю партию, а 13‑ю, 14‑ю или 15‑ю партию (на выбор); в дальнейшем опробуют по заданному циклу каждую четвертую партию.
А.10 Если в процессе опробования размах колебаний зольности партий превысит на 20% размах, заложенный в расчет, то необходимо перейти на опробование следующей ближайшей партии продукции.
А.11 При периодическом опробовании партии количество точечных проб от каждой опробуемой партии определяют по 4.5.
При периодическом опробовании отдельных вагонов:
- от каждого вагона, подлежащего опробованию, отбирают такое количество точечных проб, чтобы к концу суток в пробе их было не менее требуемого по 4.5;
- обработке и анализу подвергают пробу, накопленную за сутки. Пробу накапливают в закрытой емкости с целью предотвращения потерь влаги.
Приложение Б
(справочное)
Расчет количества точечных проб в партиях, представленных транспортными единицами различной грузоподъемности
В настоящем приложении даны примеры расчета количества точечных проб при опробовании партии топлива, погруженной в транспортные средства, а также распределения рассчитанного количества точечных проб по отдельным единицам транспортной техники.
Пример
Партия необогащенного угля массой 900 т погружена в 5 вагонов грузоподъемностью 60 т и 15 вагонов грузоподъемностью 40 т. Необходимо рассчитать количество точечных проб, отбираемых из каждого вагона, и равномерно распределить точки отбора точечных проб по всей партии.
По таблице 2 устанавливают количество точечных проб, отбираемых от всей партии, — 32 точечные пробы.
Вычисляют массы топлива, погруженного в группы вагонов одинаковой грузоподъемности:
а) 60·5 = 300 т;
б) 40·15 = 600 т.
Распределяют точечные пробы пропорционально массам топлива, погруженного в группы вагонов одинаковой грузоподъемности:
а)
б)
Распределяют точечные пробы по вагонам в каждой группе:
а)
б)
Размещение точек отбора точечных проб устанавливают, руководствуясь схемой для одного вагона, приведенной в 6.3, начиная с первого вагона партии.
Пример
Партия необогащенного угля массой 520 т погружена в 4 вагона грузоподъемностью 40 т, 3 вагона грузоподъемностью 60 т и 2 вагона грузоподъемностью 90 т. Необходимо рассчитать количество точечных проб, отбираемых из каждого вагона, и распределить точки отбора точечных проб по всей партии.
По таблице 2 устанавливают количество точечных проб, отбираемых от всей партии, — 32.
Вычисляют массы топлива, погруженного в группы вагонов одинаковой грузоподъемности:
а) 40·4= 160 т;
б) 60·3=180 т;
в) 90·2 = 180 т.
Распределяют точечные пробы пропорционально массам топлива в группах вагонов одинаковой грузоподъемности:
а)
б) и в)
Распределяют точечные пробы по вагонам в каждой группе:
а)
б)
в)
Размещение точек отбора точечных проб в вагонах устанавливают, руководствуясь схемой, приведенной в 6.3, начиная с первого вагона.
УДК 662.62:620.113:006.354 | ОКС 75.160.10 |
Ключевые слова: уголь, отбор и подготовка проб, методы |